Rolls are widely used in film and sheet extruders, slitters, stretching machines, coater machines, paper making related machines, and other machines, and they are high-precision industrial components despite their simple appearances. Our technical capabilities backed up by our many years of experience working in this industry enable us to manufacture and machine rolls for any kind of application and with any level of precision.
Metal roll manufacturing
We have an integrated system capable of producing various types of rolls (such as casting rolls, knife rolls, coating rolls, and guide rolls) all in-house, from manufacturing and machining through to surface treatment and final surface finishing.
Roll manufacturing process
Types and characteristics of rolls
Casting roll
Required characteristics
Specularity, surface roughness control, cooling efficiency, etc.
Characteristics of casting rolls manufactured by Otec
- We can handle a variety of surface finishing, ranging from ultra-mirror finishing (0.05S or lower) through to various types of satin finishing.
- We can handle a variety of internal structures that enhance cooling effects, according to customer requests. (Double tube, periphery, spiral, bored, etc.)
![]() |
![]() |
Casting drum | Spiral cylinder inside a roll |
Polishing roll
Required characteristics
Specularity, surface roughness control, roll accuracy, etc.
Characteristics of polishing rolls manufactured by Otec
- We can handle a variety of surface finishing, ranging from ultra-mirror finishing (0.05S or lower) through to various types of satin finishing.
- We can handle mirror pocket finishing that aims at both blocking prevention and specularity.
- We can manufacture and machine high-precision rolls with a roll accuracy level of 2/1,000 mm or less.
- We can handle a variety of internal structures that enhance cooling effects, according to customer requests. (Double tube, periphery, spiral, bored, drilled, etc.)
![]() |
|
Mirror surface polishing roll |
Preheating and cooling rolls
Required characteristics
Cooling efficiency, heating efficiency, surface temperature uniformity, etc.
Characteristics of preheating and cooling rolls manufactured by Otec
- We can handle a variety of internal structures that enhance cooling and heating effects, according to customer requests. (Double tube, periphery, spiral, bored, etc.)
- Using our proprietary surface treatment Tfe-Lok can prevent the adhesion of dirt such as oligomers at a preheating or cooling stage. (For details, refer to the section Tfe-Lok.)
Stretching roll
Required characteristics
Specularity, surface roughness control, etc.
Characteristics of stretching rolls manufactured by Otec
- We can handle a variety of surface finishing, ranging from ultra-mirror finishing (0.05S or lower) through to various types of satin finishing.
Suction roll
Required characteristics
Machining vacuum or blowout holes
Characteristics of suction rolls manufactured by Otec
- We have a track record in machining suction rolls with 10,000 holes for use in metal foil forming lines.
- Surface roughness can be adjusted.
- Good plating can be achieved regardless of the number of holes.
Embossing roll
Required characteristics
Pattern specifications, engraving accuracy, etc.
Characteristics of embossing rolls manufactured by Otec
- We can perform a variety of embossing operations such as mill engraving and laser engraving in collaboration with our partner companies.
- We have a track record in engraving fine V-shaped grooves on rolls in the order of several microns.
Coating roll
Required characteristics
Roll accuracy, specularity, etc.
Characteristics of coating rolls manufactured by Otec
- For precision coater machines, we can manufacture rolls with high accuracy in the order of microns and with specularity having a surface roughness of 0.05S or less.
Knife roll
Required characteristics
Roll accuracy, blade edge accuracy, blade edge linearity, etc.
Characteristics of knife rolls manufactured by Otec
- We can create sharp edges by precision surface grinding for blade edges.
- We can handle rolls that allow blade edges to be attached and detached.
- We can machine rolls with high accuracy in the order of microns.
- We can maintain used rolls.
![]() |
![]() |
Blade edge of knife roll | Acute-angled knife roll |
![]() |
![]() |
Replaceable-blade knife roll | Replaceable-blade knife roll |
Rolling roll
Required characteristics
Roll accuracy, specularity, hardness, etc.
Characteristics of rolling rolls manufactured by Otec
- We can handle rolls with high accuracy in the order of 1/1,000 mm.
- We can perform ultra-mirror finishing with a surface roughness of 0.05S or less.
Guide roll
Required characteristics
Lightweight, specularity, etc.
Characteristics of guide rolls manufactured by Otec
- We can apply chrome plating directly onto aluminum rolls.
- We can manufacture and machine carbon rolls in collaboration with our partner companies.
![]() |
![]() |
Aluminum guide roll | Carbon roll Three-layer structure (carbon, copper plating, and chrome plating) |
Roll machining facilities
General-purpose lathe | 6 units (We can machine rolls with maximum dimensions of 600 mm diameter × 6,000 mm long in-house. For rolls larger than the maximum dimensions, we outsource them to our partner companies.) |
Machining center | 1 unit |
Radial drilling machine | 1 unit |
Vertical milling machine | 1 unit |
Cylindrical grinding machine | 3 unit |
Dynamic balancing machine | 1 unit |
Others | Welding equipment etc. |
Manufacturing rolling rolls
rolling rolls are mainly used as calendar rolls for finishing processes in industries such as paper making, textile, various types of film, and aluminum foils. When materials such as paper or cloth are processed, nipping them between a steel roll and an elastic roll can form them into a smooth and glossy product. It is also possible to transfer dents to an elastic roll beforehand by using an embossed steel roll, and nip a material between the elastic roll and embossed steel roll. This kind of technique is used to form products. Using rolling rolls in such a way can add a variety of values to products. We can manufacture and machine rolling rolls with maximum dimensions of 820 mm diameter x 3,800 mm long, and with a maximum weight of five tons.
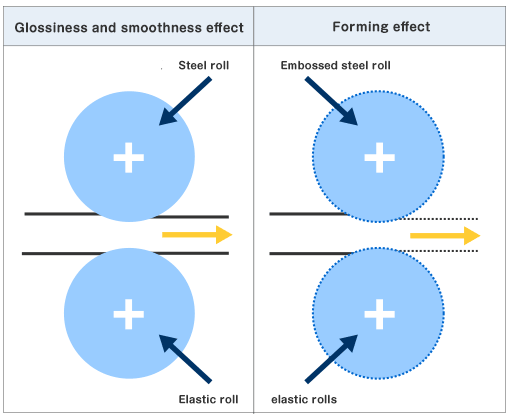
Comparison of characteristics of different rolling rolls
Type of elastic roll | Appropriate hardness Hs/D |
Maximum nipping pressure kg/cm |
Maximum speed m/min |
Effect |
New Cotton Roll | 70-80° | 250 | 300 | Glossiness effect |
Woolen Paper Roll | 82-86° | 300 | 700 | Smoothness and glossiness effect |
Special White Cotton Roll | 82-88° | 450 | 1000 | Smoothness and glossiness effect |
Milcon Paper Roll | 87-90° | 500 | 300 | Heat resistance Nipping pressure resistance |
(The figures in the table are applicable when a regular break-in is complete and load is applied evenly to rolls.)
Roll type | New Cotton Roll |
Woolen Paper Roll |
Special White Cotton Roll |
Milcon Paper Roll |
Characteristics | ||||
Maximum hardness | Hs/D 82° | Hs/D 86° | Hs/D 88° | Hs/D 91° |
Surface limit temperature | 80℃ | 80℃ | 95℃ | 130℃ |
High-speed operation resistance | × | ○ | ◎ | × |
Pressure resistance | × | △ | ◎ | ◎ |
Resiliency | ◎ | ○ | △ | × |
Heat resistance | × | × | △ | ◎ |
Smoothness | × | ○ | ◎ | ○ |
Durability | △ | ○ | ◎ | × |
Break-in period | Long | Long | Short | Short |
Quality variation | △ | ○ | ◎ | ◎ |
Hardness variation | △ | ○ | ◎ | ◎ |
Washability | ◎ | △ | △ | × |
Glossiness/temperature evenness | △ | ○ | ◎ | ◎ |
(◎: Excellent, ○: Good, △: OK, ×: No good)
