We always conduct new technological developments such as internal research experiments and industry-university-government collaboration projects with public research organizations and universities. Our research laboratory is equipped with a variety of experimental devices and measuring instruments to improve the functionality of plating surfaces and develop high value-added surface treatments.
Joint developments
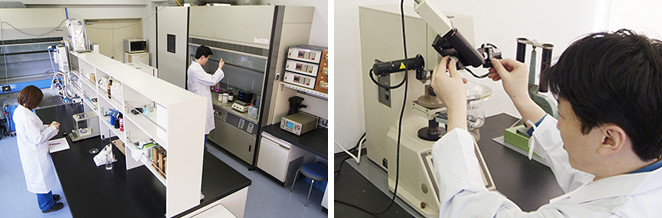
We have a track record in joint technological developments with a large number of companies. If you have any needs related to roll manufacturing or plating, please feel free to consult with us. We will be pleased to prepare effective proposals or participate in joint technological developments, based on the expertise we have cultivated over many years.
Track record in R&D
2015
Received the 2014 supplementary subsidy for manufacturing, commerce, and service innovation “Prototype development of chrome plating impregnated with fluorocarbon polymers” (Part of the development was outsourced to Technology Research Institute of Osaka Prefecture)
We conducted research with the aim of developing functional plating films with excellent lubricity, mold releasability, and durability by impregnating hard chrome plating (with high hardness and high wear resistance) with various types of fluorocarbon polymers.
2014
Received the 2013 subsidy for manufacturing, commerce, and service innovation projects for small and medium-sized enterprises and small businesses “Enhancing the ultra-scale mirror grinding technique for chrome-plated rolls”
We conducted R&D with the aim of producing higher-performance mirror finished rolls by enhancing the surface grinding technique for ultra-scale mirror finished rolls for manufacturing optical plastic films that are used for LCD televisions, smartphones, and other devices.
2013
Received the 2012 subsidy for supporting prototype development and other manufacturing projects for small and medium-sized enterprises and small businesses “Prototype development of hard trivalent chromium plating with excellent lubricity, mold releasability, and wear resistance” (Part of the development was outsourced to Technology Research Institute of Osaka Prefecture)
We considered that conjugating hard trivalent chromium plating films with fine particles would make it possible to produce better properties such as lubricity, mold releasability, and wear resistance than normal chrome plating. We conducted research with the aim of improving the functionality of hard trivalent chromium plating by using this method.
2009
Received the 2009 subsidy for supporting product development and other manufacturing projects for small and medium-sized enterprises “Prototype development of hard trivalent chromium plating” (Part of the development was outsourced to Tokyo City University and Technology Research Institute of Osaka Prefecture)
We established analytical methods for plating solutions, assessed the physical properties of plating films, and disseminated technical information to customers in order to make practical use of industrial chrome plating (hard trivalent chromium plating) from trivalent chromium baths.
2007
2007 R&D by regional regeneration consortiums “Development of an environmentally friendly hard chrome plating system free of hexavalent chromium” (Joint project by Musashi Institute of Technology and eight private enterprises)
2006
2006 R&D by regional regeneration consortiums “Development of an environmentally friendly hard chrome plating system free of hexavalent chromium” (Joint project by Musashi Institute of Technology and eight private enterprises)
We conducted research on practical uses of industrial chrome plating from trivalent chromium baths. As a result, we succeeded in plating on small rolls and other materials. The physical properties of hard chrome plating free of hexavalent chromium were slightly inferior to those of industrial chrome plating from hexavalent chromium baths, but we considered that it was quite possible to make practical use of this plating for industrial applications, and we planned to continue our R&D on this project.
2004
2004 R&D by regional regeneration consortiums “Research on practical uses of alloy plating containing phosphorus as an alternative plating to hexavalent chromium plating” (Joint project by Technology Research Institute of Osaka Prefecture and four private enterprises)
2003
2003 R&D by regional regeneration consortiums “Research on practical uses of alloy plating containing phosphorus as an alternative plating to hexavalent chromium plating” (Joint project by Technology Research Institute of Osaka Prefecture and four private enterprises)
We developed Ni-W-P alloy plating as an alternative plating to hexavalent chromium plating and Cr-P-C alloy plating from trivalent chromium baths, and conducted research on practical uses of these platings.
2002
2002 Osaka core research projects “Development of more advanced plating processes” (Joint project by Technology Research Institute of Osaka Prefecture and 11 private enterprises)
2001
2001 Osaka core research projects “Research on more advanced plating processes” (Joint project by Technology Research Institute of Osaka Prefecture and 14 private enterprises)
Under the theme of environmentally friendly plating processes free of waste plating solutions, we conducted a variety of research, including the application of ion exchange membrane processes to various types of plating, plating baths free of waste plating solutions, sludge reduction, stabilization of plating solution compositions in plating baths, improvement of plating film quality, development of new alloy plating, and continuous plating.