Highly corrosion-resistant chrome plating Chroston is a non-crack plating free of cracks and pits that occur in normal chrome plating layers.
Characteristics of Chroston
Chroston has a special crystal structure that does not cause cracks or pinholes.
Chroston provides good corrosion resistance because it has no cracks. Sufficient corrosion resistance can be expected from single-layer plating with a thickness of 20 μm or more. However, Chroston cannot be used in environments where chrome plating is melted or corroded.
Rusting tests to examine the relationship between plating thickness (μm) and salt water spraying time (hours)
The following photos show the results of tests spraying salt water onto Chroston (photos in the upper row) and normal chrome plating (photos in the lower row) applied to steel materials. Chroston does not rust at a thickness of 15 μm or more even after 3,000 hours, proving that it is highly corrosion resistant. Corrosion resistance cannot be expected from normal hard chrome plating even if thick plating is applied.
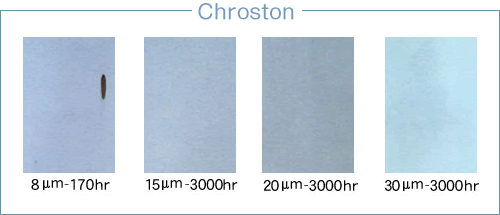
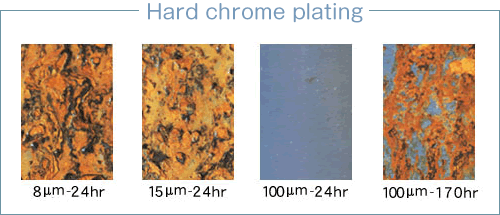
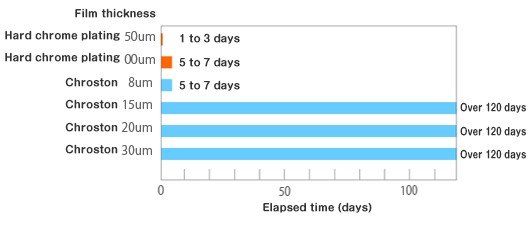
The hardness of Chroston is approximately Hv600 to Hv700, which is lower than the hardness of normal hard chrome plating.
Heating Chroston above 400°C sharply drops its hardness.
The glossiness of Chroston is different from that of normal chrome plating.
Chroston can be detached and replated in the same way as normal chrome plating.
The glossiness of Chroston is adjustable.
Materials that can be plated
Chroston can be applied to a wide range of metal materials including steel, stainless steel, aluminum, copper, and copper alloys.
Uses of Chroston
Chroston has been used for applications that cannot expect sufficient corrosion resistance from normal hard chrome plating and applications that require glossiness adjustment.
- Anti-rust undercoating for hard chrome plating
- Various engraved and embossing rolls whose glossiness changes are regarded as important
- Glass and plastics forming molds and parts that require heat resistance or corrosion resistance
- Stainless steel parts that must prevent crevice corrosion, pitting corrosion, intergranular corrosion, and other corrosions, such as valve stems, and pump shafts that are used in sea water, on the beaches, or under similar environments
- Parts that cause high-temperature corrosion such as sulfide corrosion or vanadium corrosion
- Parts that aim to prevent gas corrosion
- Parts that require oxidation resistance
- Parts that aim to prevent corrosion in a humid atmosphere
![]() |
|
Embossing roll coated with Chroston |