Hard chrome plating, also referred to as industrial chrome plating, is a representative industrial plating that has a number of excellent mechanical properties such as wear resistance, corrosion resistance, and mold releasability.
Characteristics of hard chrome plating
Generally, the hardness of hard chrome plating is Hv700 or higher.
Otec provides high-rigidity plating with a hardness of Hv900 or higher by adjusting the liquid composition.
Hardness of various plating films and metal materials
Plating and steel types | Hardness (Hv) |
Chroamor (Otec proprietary plating) | 1500-1800 |
Chrome plating | 800-1000 |
Nickel plating | 400-500 |
Nickel-phosphorus plating | 400-500 |
Nickel-phosphorus plating (with heat treatment) | 800-1000 |
Copper plating | 60 |
Zinc plating | 40 |
Aluminum and aluminum alloy | 20-140 |
Medium carbon steel (with quenching and tempering) | 160-285 |
Austenitic stainless steel | 200-260 |
Chromium-molybdenum steel | 245-440 |
Comparison of the hardness of various metals produced by metallurgical processes and electrodeposition
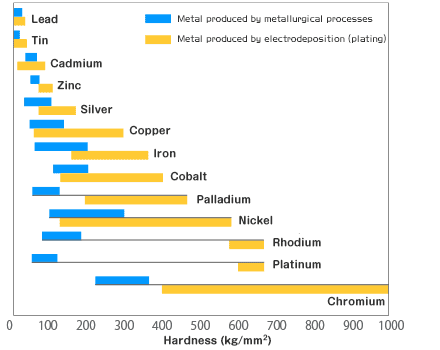
Hard chrome plating features a small coefficient of friction, which means excellent wear resistance.
Heating hard chrome plating above 400℃ sharply drops its hardness. At Otec, the baking process for removing hydrogen after plating is performed under strict temperature control by using a dedicated furnace.
Change in the hardness of chrome plating during heating (heating time: 3 hours)
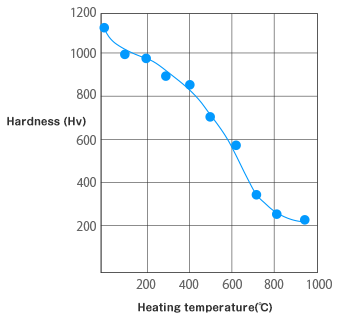
Hard chrome plating is stable against chemicals other than chlorides.
The treatment temperature of hard chrome plating is as low as approximately 50°C, which means that there is almost no thermal influence on materials.。
The surface roughness of the workpiece to be plated can be freely adjusted. (Ultra-mirror finish (0.05S or lower), satin finish (matte finish), semimatte finish, mirror pocket finish, etc.)
Hard chrome plating ensures dimensional accuracy and allows replating and partial plating (overlaying).
Using nickel plating as an undercoating improves the corrosion resistance of hard chrome plating.
Materials that can be plated
Hard chrome plating can be applied to a wide range of metal materials including steel, stainless steel, aluminum, copper, copper alloys, nickel, and titanium.
Uses of hard chrome plating
Various rolls, various molds, cylinders, pistons, piston rods, various shafts, coater bars, etc.
Chrome-plated roll for manufacturing optical films
Chrome plating on coater bar
Facilities related to hard chrome plating
Plating bath Total amount of liquid |
11 baths Approx. 120,000 liters |
Rectifier | 23 units (total quantity of electricity: approx. 83,000 A) |
Crane | 10-ton crane etc. |
Cylindrical buffing machine | 7 units (max. 850 mm diameter × 6,000 mm long) |
Internal diameter buffing machine | 2 units |
Liquid honing equipment | 1 unit |
Large baking furnace | 2 units (internal dimensions: 1,600 mm W × 5,300 mm L × 1,400 mm H) |
Note: We also accept a job request for only heat treatment. |