Based on many years of experience and technologies, Otec applies coherent plating to difficult-to-plate materials such as aluminum and titanium.
Chrome plating on aluminum
Because aluminum and aluminum alloys are lightweight, relatively strong, and inexpensive, they are widely used in a variety of areas. However, aluminum and aluminum alloys are very soft materials, so that they are subject to anodization treatment, but their hardness is still inadequate in many cases. In particular, for components that become significantly worn or require durability, mold releasability, or surface smoothness, these properties can be assigned to aluminum surfaces by applying chrome plating. However, if aluminum alloys contain much silicon or similar substances, their adhesiveness will decline. The tables below compare the hardness of different materials and show the adhesiveness of chrome platings on different aluminum materials. These tables can be used as a general guide. Based on our advanced expertise and many years of experience, we apply chrome plating that can successfully adhere directly to almost all aluminum materials.
Adhesiveness of chrome plating on different aluminum materials
Material Hardness (Hv) |
A1100 | A2017 | A5052 | Medium carbon steel | Stainless steel | Chrome plating |
30 | 150 | 60 | 140-240 | 200-260 | 800-1000 |
Wrought alloy | A1100 | A2000 | A3000 | A4000 | A5000 | A6000 | A7000 |
◯ | ◯ | ◯ | × | ◯ | ◯ | × |
Casting alloy | AC1A,B | AC2A,B | AC3A | AC4A,B | AC4C,CH,D | AC5A | AC7A | AC8 AB,C |
AC9A,B |
◯ | △ | × | × | △ | ◯ | ◯ | × | × |
Die casting alloy | ADC1 | ADC3 | ADC5 | ADC6 | ADC10,10Z | ADC12,12Z | ADC14 |
× | × | ◯ | ◯ | △ | × | × |
Adhesiveness → ◯:Good, △:No good, ×:Bad
(Otec chrome plating shows all good results except for A7000.)
(Otec chrome plating shows all good results except for A7000.)
![]() |
![]() |
Roll for smoothing out wrinkles | Heat sealer |
Chrome plating on titanium
Titanium and titanium alloys have a low specific gravity, high strength, and excellent corrosion resistance, thus enabling them to be used in a variety of areas. For example, titanium and titanium alloys are used in aircraft parts, automobile parts, chemical plant components, heat exchangers, condensers, electrodes, artificial bones, as well as our familiar goods such as golf clubs, eyeglass frames, and watch frames. However, because their hardness is low and their wear resistance is weak, they tend to seize easily, making it difficult to use them in sliding parts. For this reason, hard chrome plating is commonly applied to titanium and titanium alloys in order to improve their wear resistance. Titanium has high chemical activity and so it is very difficult to secure the adhesiveness of plating on titanium, but we have succeeded in good adhesion of chrome plating onto titanium surfaces by applying special treatment. This success enables us to handle partial plating and replating easily and add durability to titanium materials. For applications that require seizure prevention or low friction, we can use Tfe-Lok, a composite plating of chromium and PTFE.
Material properties of titanium and chrome plating
Tensile strength (kgf/mm2) |
Hardness (Hv) |
Elongation (%) |
Specific gravity (g/cm3) |
Electrical conductivity (Steel100%) |
Thermal conductivity (CGS unit) |
Coefficient of thermal expansion | |
Chrome plating | 8-70 * |
800-1000 | 0 | 7.2 | 3.5 | 0.17 | 6.5 |
99.7%Ti | 35 | 160 | 40 | 4.51 | 3.6 | 0.04 | 8.4 |
Ti-6AI-4V | 94 | 340 | 11 | 4.43 | 1.0 | 0.02 | 9.0 |
1100 aluminum alloy | 16.9 | 30 | 5 | 2.71 | 57 | 0.52 | 23.6 |
7075 aluminum alloy | 58.3 | 150 | 11 | 2.80 | 30 | 0.29 | 23.6 |
Hot rolled steel | 42.0 | 140-240 | 30 | 7.85 | 12 | 0.14 | 11.7 |
Stainless steel | 63 | 200-260 | 55 | 7.9 | 2.4 | 0.04 | 17.3 |
* indicates adhesion force.
![]() |
![]() |
Shafts made of pure titanium and titanium alloy | Titanium golf club head |
Chrome plating on stainless steel
Stainless steel has excellent corrosion resistance as it forms passivation films on its surfaces, thus enabling it to be widely used in a variety of areas. However, stainless steel causes localized corrosion such as pitting corrosion or crevice corrosion, depending on the environment where it is used. Results of investigations on the use of stainless steel over a number of years (percentage of accidents according to corrosion types) indicate that 70% to 80% of accidents resulted from localized corrosion, and there are many cases where materials reach the end of their life due to localized corrosion rather than general corrosion. This means that steel type selection, structural consideration, surface treatment, and other measures are important factors to prevent corrosion.
A creviced structure with an interface between metal materials or between a metal material and a non-metal material causes more significant localized corrosion than other portions. Stainless steel surfaces are protected with a very thin passivation film, but this passivation film will be destroyed and melted away if sufficient oxygen is not supplied through a creviced structure, changes occur to a solution environment, or an oxidizing substance such as chlorine ion exists in an environment. For these reasons, chrome plating is sometimes applied directly to stainless steel to prevent corrosion. However, if normal chrome plating is applied to stainless steel, cracks that exist on the plating film allow passivation film destruction factors such as chlorine to easily penetrate through the film and accumulate on the stainless steel. This causes corrosion to reach the substrate, resulting in plating films being peeled off or some other problem occurring. Applying Otec’s crack-free chrome plating Chroston can prevent such corrosion from progressing.
Chroston is applied to valve stems of pipes used on the beach or in seawater and to seal liners in contact with seal lips on stern tube oil seal devices in ships in order to prevent pitting corrosion and crevice corrosion on valve stems and seal liners from progressing as well as to protect valve stems, seal liners, and seal lips from damage. Using Chroston can extend the service lives of parts that produce many problems with normal chrome plating, thus resulting in Chroston being highly regarded by its users.
A creviced structure with an interface between metal materials or between a metal material and a non-metal material causes more significant localized corrosion than other portions. Stainless steel surfaces are protected with a very thin passivation film, but this passivation film will be destroyed and melted away if sufficient oxygen is not supplied through a creviced structure, changes occur to a solution environment, or an oxidizing substance such as chlorine ion exists in an environment. For these reasons, chrome plating is sometimes applied directly to stainless steel to prevent corrosion. However, if normal chrome plating is applied to stainless steel, cracks that exist on the plating film allow passivation film destruction factors such as chlorine to easily penetrate through the film and accumulate on the stainless steel. This causes corrosion to reach the substrate, resulting in plating films being peeled off or some other problem occurring. Applying Otec’s crack-free chrome plating Chroston can prevent such corrosion from progressing.
Chroston is applied to valve stems of pipes used on the beach or in seawater and to seal liners in contact with seal lips on stern tube oil seal devices in ships in order to prevent pitting corrosion and crevice corrosion on valve stems and seal liners from progressing as well as to protect valve stems, seal liners, and seal lips from damage. Using Chroston can extend the service lives of parts that produce many problems with normal chrome plating, thus resulting in Chroston being highly regarded by its users.
Mechanism of crevice corrosion
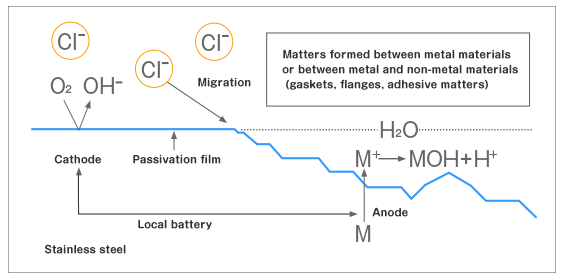